Helical Piers
Helical piers are deep foundation elements that are designed for new construction or repair elements. Helical piers are designed based on the weight of the structure, as well as loads introduced to the structure from external forces; such as, wind, snow and seismic activity. The diameters of the helical plates on the pier is designed for the given loading and soils conditions. The allowable capacity of each pier is directly correlated to the minimum installation torque. Straight Line Construction/Ram Jack Companies utilize calibrated monitoring equipment to verify installation torque in the field. Since installation torque directly relates to working capacity of the element, the minimum specified installation torque must always be obtained in the field to achieve desired working capacity. The minimum installation torque requirement sometimes requires use of piers with larger helices than initially designed for the project, as many times repairs are designed without adequate geotechnical data for the location. Piers with multiple helical plates may also be required to achieve minimum specified installation torque where higher loads or softer soils are encountered.

Installation torque can be verified by either converting installation pressure to torque or using calibrated monitoring equipment with direct torque readings. In either system, the torque heads are calibrated yearly to ensure that each installation meets the minimum torque values specified to meet the design working capacity.
​
On repair projects that require elevation recovery due to settlement of the structure, an initial floor level survey is conducted with a Ziplevel. A Ziplevel is a pressurized hydrostatic altimeter and works by measuring the difference in elevations between the base unit and the handheld unit. Negative elevations referenced are below the basepoint, and positive elevations are higher than the basepoint. Measurements are monitored and recorded during the lifting process while attempting maximum practical recovery. A Final Floor Level survey is recorded to document the new elevations of the structure.
​
​For large scale projects, the helical installation torque may be verified with a pre-production verification test. Pre-production verification test elements are installed to a specified torque value correlating to an ultimate load capacity of 200% of the design load of the helical pier element. The elements are loaded either in tension or compression through a test beam and a calibrated center-hole hydraulic jack while monitoring the movement of the element with dial indicators at the top of the jacking equipment. The tests are loaded incrementally to 200% of the design load and then unloaded to determine the rebound of the element to calculate how much movement was permanent set (soil compression) and how much was elastic (elongation of the steel element) to determine the depth of the load transfer and determine if the permanent movement is acceptable. Compression verification tests conform to ASTM D1143 and tension Verification tests conform to ASTM D3689.
Micropiles
Micropiles are composite deep foundation elements that consist of reinforcing steel and/or casing and grout. The geotechnical capacity of a micropile is dictated by the various geotechnical strata that the pile is being installed in, drilling means and methods, drill bit type and drill hole diameter. The structural capacity of a micropile is readily quantifiable based on the drill hole diameter, grout strength, steel reinforcing bar grade and diameter, and steel casing if required. However, the geotechnical capacity can vary greatly based on soil or rock conditions as well as installation means and methods; therefore, a pre-production verification test is necessary prior to installing production micropiles to verify the grout-to-ground bond capacity assumed in the design. A pre-production micropile verification test consists of an on-site sacrificial micropile installation that mimics the same drilling means and methods for the production micropiles.
​
Like helical pier verification testing; micropiles are tested to 200% of the design load in accordance with NHI-05-039, “Design and Construction of Micropiles”. The verification test is a cyclic test that includes a minimum 10-minute creep holds at 130% of design load to determine if movement over time is increasing or decreasing. If during the 10-minute creep holds, the pile experiences no more than 0.040” of movement, the creep test is discontinued and the balance of the load cycles are performed until the end of the test. If the movement exceeds 0.040” in 10 minutes, the creep test is extended an additional 50 minutes. The total movement cannot exceed 0.080” in the entire 60-minute hold period, or the pile is deemed unacceptable. After the pile is loaded to 200% of the design load, it is unloaded back to a 5% alignment load, where permanent (residual) movement is determined. The difference between total movement at 200% design load and permanent movement at alignment load gives the elastic movement. This is useful in back calculating the apparent free length of the micropile element to determine what depth the load transfer occurs in the micropile. The verification test verifies that there is an acceptable factor of safety for the grout-to-ground bond capacity used in design.

Typical micropile tension test setup
​
In addition to verification tests, proof tests are also frequently performed on production micropiles. Proof testing is typically performed on approximately 5% of the production micropiles. Proof tests are generally taken to a load corresponding to 160% of the design load, to confirm that installation means and methods are viable across the entire site. Both verification and proof tests can be tested in either tension or compression. Tension tests are generally more economical due to quicker setup. For tension testing, bearing pads generally consisting of timer beams and wood blocks are placed on either side of the test beam and a center hole hydraulic jack is placed on top of the test beam. The pile is then loaded in tension and the reaction forces are transferred through the bearing pads to the ground surface. Compression tests are more expensive and generally takes longer as they require the installation of reaction piles. The setup for testing piles in compression is similar to testing in tension except the jack is placed on the bottom of the beam and the test element is loaded in compression with the reaction elements resisting the jacking forces.
​
In addition to verifying the grout-to-ground bonding capacity through load testing, there are strict quality control measures taken to verify the grout strength. Traditionally, 3rd party testing facilities will sample the production grout and make 2”x2”x2” grout cubes in the field. The grout cubes are then tested for compressive strength in accordance with ASTM C109. Grout cubes are typically tested at 3, 7, 14- and 28-day intervals to confirm the compressive strength of the grout, as the grout is a key component in the structural capacity of the micropile. Straight Line Construction takes it a step further and uses a Mud Balance to verify the specific gravity of each hopper of grout batched. Ideally, the specific gravity for structural grout is between 1.80 and 1.90 which correlates to a water to cement ratio of 0.45 to 0.4 respectively. Since the grout typically used for micropiles is a simple water and cement grout, the specific gravity of the grout relates directly to the water/cement ratio and corresponding compressive strength of the grout. A study was conducted with CTL Thompson-Pueblo, Printz Engineering Services, LLC and Straight Line Construction during the micropile installation at the CSU Pueblo Academic Resources Center. Mud balance testing was performed on each batch of grout and the results were compared to the compressive strength test results from the grout cubes. Samples with specific gravities of 1.80 to 1.90 consistently yielded compressive strengths in excess of 3,000 psi in three days (data is available upon request). Performing mud balance testing of each grout batch helps to immediately ensure that quality structural grout is consistently being used, prior to receiving compressive strength results.
Soil Nails
Soil nails are in-situ soil reinforcement that consists of a steel reinforcing bar inside of a grout column in a slightly inclined hole. Soil nails are useful for vertical, top down construction shoring or slope stabilization. Soil nail reinforcing bars may consist of Grade 75 bar in accordance with ASTM A615, 150 KSI bar in accordance with ASTM A722 or hollow bar with minimum yields of 85 KSI in accordance with ASTM A513 or A519.
​
Soil nail pull-out testing is verified on pre-production sacrificial soil nails to a VTL (Verification Test Load) per FHWA-NHI-14-007, “Soil Nail Design and Construction Manual, GeoCircular #7”. The test verifies that the design assumptions used for pullout in design of the soil nail structure are valid with an acceptable factor of safety. Production nails are installed after proving soil-to-grout bonding capacities through verification testing. Proof tests are typically performed on 5% of the production nails on the wall, to verify geotechnical conditions have not changed significantly and that drilling means and methods are still applicable to site conditions.
​
Soil nail grout is also tested for compressive strength in accordance with ASTM C109, typically by a 3rd party testing laboratory. Straight Line Construction/Ram Jack Companies utilize a mud balance to verify the specific gravity of each hopper of grout batched. Ideally, the specific gravity for structural grout is between 1.80 and 1.90 which correlates to a water to cement ratio of 0.45 to 0.4 respectively. Since the grout typically used for soil nails is a simple water and cement grout, the specific gravity of the grout relates directly to the water/cement ratio and corresponding compressive strength of the grout. A study was conducted with CTL Thompson-Pueblo, Printz Engineering Services, LLC and Straight Line Construction during the micropile installation at the CSU Pueblo Academic Resources Center. Mud balance testing was performed on each batch of grout and the results were compared to the compressive strength test results from the grout cubes. Samples with specific gravities of 1.80 to 1.90 consistently yielded compressive strengths in excess of 3,000 psi in three days (data is available upon request). Performing mud balance testing of each grout batch helps to immediately ensure that quality structural grout is consistently being used, prior to receiving compressive strength results.
Tieback Anchors
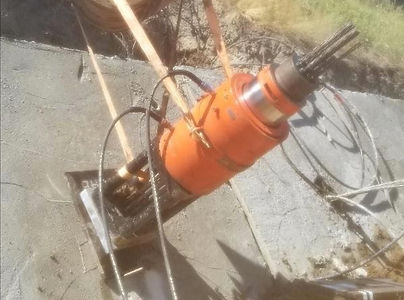
Typical Test and Lock-off setup
​
Tieback Anchor grout is also tested for compressive strength in accordance with ASTM C109, typically by a 3rd party testing laboratory. Straight Line Construction/Ram Jack Companies utilize a mud balance to verify the specific gravity of each hopper of grout batched. Ideally, the specific gravity for structural grout is between 1.80 and 1.90. Since the grout typically used for tieback anchors is a simple water and cement grout, the specific gravity of the grout relates directly to the water/cement ratio and corresponding compressive strength of the grout. A study was conducted with CTL Thompson-Pueblo, Printz Engineering Services, LLC and Straight Line Construction during the micropile installation at the CSU Pueblo Academic Resources Center. Mud balance testing was performed on each batch of grout and the results were compared to the compressive strength test results from the grout cubes. Samples with specific gravities of 1.80 to 1.90 consistently yielded compressive strengths in excess of 3,000 psi in three days (data is available upon request). Performing mud balance testing of each grout batch helps to immediately ensure that quality structural grout is consistently being used, prior to receiving compressive strength results.
Tieback anchors are actively loaded anchors that can be used for excavation support, landslide mitigation, tiedowns, and permanent shoring walls. Tieback anchors may be single element 150 KSI solid bar anchors in accordance with ASTM A722, or multi-strand 270 KSI 7-wire strand in accordance with ASTM A416. Anchors in excess of 50’ in length are typically multi-strand anchors, for ease of installation and reduced weight of the multi-strand package versus solid bar reinforcing.
​
Preproduction verification test is performed prior to installation of production anchors. Verification, performance and proof tests are all tested in accordance with FHWA-IF-99-015, GeoCircular No. 4, “Ground Anchors and Anchored Systems”. Preproduction verification tests are typically run to 133% of anchor design load, unless the bond length is in material that is susceptible to creep, where the anchor would be tested to 150% of design load. The preproduction verification test is a cyclic test with a minimum 10-minute creep test at the maximum test load. If the creep does not exceed 0.040” in 10 minutes, it is discontinued; if it exceeds 0.040” in 10 minutes the test is extended another 50 minutes. The total creep cannot exceed 0.080” for the entire 60-minute hold or else the anchor is considered unacceptable. After the creep test, the anchor is unloaded back to the initial alignment load and a permanent movement reading is taken. The difference between the total movement at maximum test load and the permanent movement at alignment load yields the total elastic movement the anchor experienced during the test. The elastic movement can be used to determine the apparent free length of the tieback anchor. The anchor must de-bond 80% of the unbonded length, but no more than the unbonded length plus 50% of the bond length to be considered acceptable.
​
Performance tests are cyclic load test identical to the pre-production verification test, except they are performed on production anchors. All the same acceptance criteria apply to the performance test that apply to the verification test. Typically, 5% of the production anchors are subjected to performance testing on a project. After a performance test is deemed acceptable, the anchor is typically loaded to 70% of ultimate and locked off at that load. The typical design load of an anchor does not exceed 60% of the anchor ultimate strength and locking off 10% higher allows for some losses in prestress force.
​
The balance of the anchors that are not subject to performance testing are proof tested. The proof test is not a cyclic loading schedule, as the load is advanced directly to the creep load at 133% or 150% of design load, is held for the creep portion of the test and unloaded to the initial alignment load for the permanent movement reading. The anchor is then loaded to70% of ultimate load and locked off.
Compaction Grouting
Compaction Grouting is a ground improvement technique for increasing both the density and strength of foundation soils in place by injecting stiff, low mobility grout through casing that is driven or drilled into the soil. Compaction grouting is typically performed in a bottom up manner where the grout tube is advanced full depth and the grout is placed starting from the bottom of the treatment depth. As the grout is injected under pressure, the grout forms a bulb at the end of the injection pipe. As the injection continues, the bulb volumetrically enlarges, displacing and densifying the surrounding soils. The extent and degree of soil densification depends on the spacing of the grout injection points, grout injection pressures, relative density of the existing soils, and the spacing of injection points. The consistency of the grout and the volume of grout injected also impacts the extent of soil densification.
​
Quality Control and Assurance of compaction grouting consists of monitoring the volume of grout per foot of each individual column injected. Typical grout takes are on order of 2-5 cubic feet of grout per vertical foot of grout column. As the casing is extracted in one-foot intervals, the grout yield is monitored carefully until the top of the column reaches the bottom of the structure. Controlled elevation recovery of existing structures can be accomplished using this technique by grout injecting beyond the state where soil densification is achieved. When the pressure of the grout mass exceeds the overburden pressure, the weight of the structure and the shear strength of the soil cone above the injection point, the soil shears and the grout pressure will lift the soil and the structure supported on it. Floor level surveys are commonly performed prior to and after compaction grouting. Elevations are also typically monitored during compaction grouting to monitor and minimize unwanted movement.
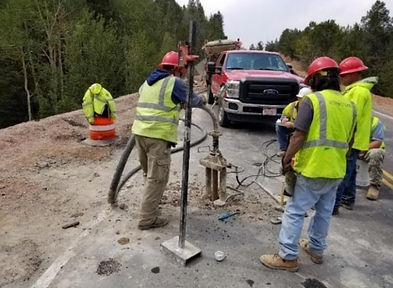

Mud Jacking / Slab Jacking
Mudjacking, or slabjacking, involves drilling 1 ¾” holes into the concrete and injecting a cementitious grout slurry consisting of water, sand and cement under the slab. The injected grout first fills the voids under the slab and once filled, additional grout is injected creating enough pressure to recover the slab up to its original elevation as much as the slab will allow. Mudjacking/Slabjacking is an effective technique for raising lightly loaded concrete flatwork (sidewalks, driveways, garage floors, patios, porches, etc.). Elevations are monitored with a Ziplevel during the repair to determine when the appropriate recovery has been achieved.
Poly Foam Injection
Polyurethane Foam Injection takes the original concept of Mudjacking/Slabjacking with cementitious material and combines it with the use of high-density, low-weight, expansive polyurethane foam to recover slabs back to a desired elevation. Small diameter holes are drilled into the concrete slab and structural grade polyurethane foam is injected into the void below the slab. After the void is filled, the expanding properties of the polyurethane foam creates pressure resulting in recovery of the concrete slab. Elevations are monitored during treatment with a Ziplevel to determine when appropriate lift has been achieved.